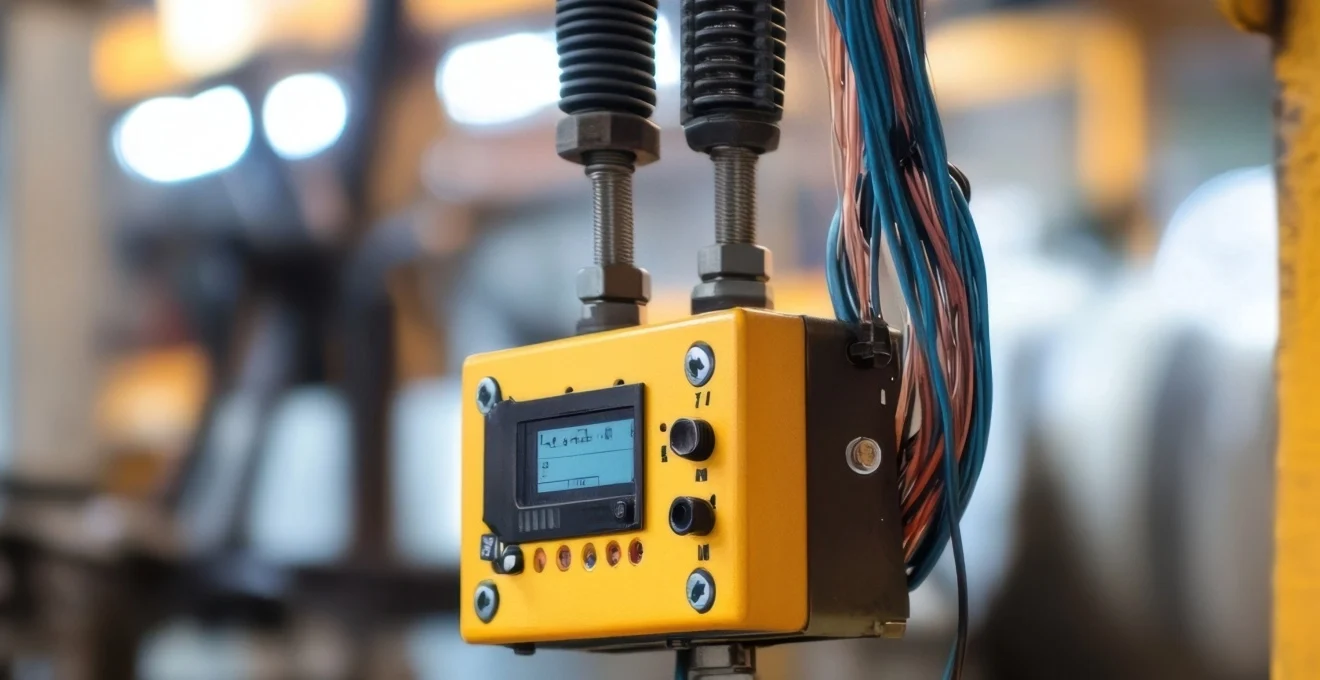
Dans le monde industriel moderne, la mesure précise de la température joue un rôle crucial pour assurer l'efficacité, la sécurité et la qualité des processus. Au cœur de cette mesure se trouve le capteur de température , un dispositif indispensable dans de nombreux secteurs. Ces capteurs permettent de surveiller en temps réel les variations thermiques, offrant ainsi un contrôle optimal des équipements et des environnements. Que ce soit dans l'industrie manufacturière, l'agroalimentaire ou les systèmes de chauffage, ventilation et climatisation (CVC), les capteurs de température sont les yeux et les oreilles des systèmes de contrôle, garantissant le bon fonctionnement des opérations.
Comprendre le fonctionnement des capteurs de température
Les capteurs de température sont des dispositifs ingénieux conçus pour détecter et quantifier les changements de température dans leur environnement immédiat. Leur fonctionnement repose sur des principes physiques bien établis, exploitant les propriétés thermiques des matériaux pour traduire les variations de température en signaux mesurables. Cette capacité à convertir une grandeur physique en données exploitables est au cœur de leur utilité dans de nombreux domaines industriels et scientifiques.
Mesurer les variations thermiques avec précision
La précision est la pierre angulaire de tout capteur de température efficace. Ces dispositifs utilisent divers phénomènes physiques pour détecter les changements de température. Certains exploitent la dilatation thermique des métaux, tandis que d'autres se basent sur les variations de résistance électrique ou la génération de tensions thermoélectriques. Par exemple, les thermocouples, largement utilisés dans l'industrie, génèrent une tension proportionnelle à la différence de température entre deux points de jonction de métaux différents.
La sensibilité d'un capteur détermine sa capacité à détecter de infimes variations de température. Les capteurs modernes peuvent atteindre des précisions remarquables, certains étant capables de mesurer des écarts de l'ordre du millième de degré Celsius. Cette précision est cruciale dans des applications telles que la recherche scientifique ou les processus industriels de haute précision.
Transmettre les données à un système de contrôle
Une fois la température mesurée, le capteur doit communiquer cette information au système de contrôle. Cette transmission se fait généralement sous forme de signal électrique. Selon le type de capteur, ce signal peut être analogique (une tension ou un courant variable) ou numérique (une série de données binaires).
Dans les systèmes industriels modernes, ces signaux sont souvent traités par des automates programmables industriels (API) ou des systèmes de contrôle distribué (DCS). Ces unités de contrôle interprètent les données de température et les utilisent pour prendre des décisions en temps réel, ajustant les paramètres du processus si nécessaire.
La qualité de la transmission des données est aussi importante que la précision de la mesure elle-même. Un signal propre et stable est essentiel pour garantir la fiabilité du contrôle de température.
Choisir entre capteurs analogiques et numériques
Le choix entre capteurs analogiques et numériques dépend largement de l'application spécifique et de l'infrastructure existante. Les capteurs analogiques offrent une réponse continue et peuvent être plus simples à intégrer dans certains systèmes existants. Ils sont souvent préférés dans des applications où une réponse rapide est cruciale.
Les capteurs numériques, quant à eux, présentent plusieurs avantages. Ils sont généralement plus résistants aux interférences électromagnétiques et peuvent transmettre des données sur de plus longues distances sans perte de précision. De plus, ils peuvent souvent être configurés et étalonnés à distance, ce qui simplifie la maintenance.
Certains capteurs modernes, appelés capteurs intelligents
, intègrent des capacités de traitement avancées. Ils peuvent effectuer des calculs, appliquer des corrections et même prendre des décisions basiques directement au niveau du capteur, réduisant ainsi la charge de travail du système de contrôle central.
Explorer les types de capteurs selon les technologies
La diversité des applications de mesure de température a conduit au développement de plusieurs types de capteurs, chacun exploitant des principes physiques différents. Cette variété permet de répondre aux exigences spécifiques de chaque environnement, qu'il s'agisse de mesurer des températures extrêmes dans un four industriel ou de surveiller avec précision la température d'un processus chimique délicat.
Utiliser les thermocouples dans les environnements extrêmes
Les thermocouples sont parmi les capteurs de température les plus polyvalents et les plus largement utilisés dans l'industrie. Leur principe de fonctionnement, basé sur l'effet Seebeck, leur permet de mesurer une large gamme de températures, allant de -270°C à plus de 2000°C pour certains modèles.
Cette capacité à fonctionner dans des conditions extrêmes fait des thermocouples le choix privilégié pour des applications telles que :
- La surveillance des fours industriels
- Le contrôle des processus métallurgiques
- La mesure des gaz d'échappement dans l'industrie automobile
Les thermocouples sont appréciés pour leur robustesse, leur temps de réponse rapide et leur coût relativement faible. Cependant, ils nécessitent une compensation de la jonction froide et peuvent être moins précis que d'autres types de capteurs sur des plages de température plus étroites.
Adopter les sondes à résistance pour les mesures stables
Les sondes à résistance, également connues sous le nom de RTD (Resistance Temperature Detector), offrent une excellente stabilité et une précision supérieure sur une plage de température modérée. Elles fonctionnent sur le principe de la variation de la résistance électrique d'un métal pur (généralement du platine) en fonction de la température.
Les RTD sont particulièrement appréciées dans les applications nécessitant une grande précision et une stabilité à long terme, telles que :
- Le contrôle de processus dans l'industrie chimique
- La surveillance de la température dans les équipements de laboratoire
- Les systèmes de calibration de haute précision
Bien que plus coûteuses que les thermocouples, les sondes à résistance offrent une meilleure linéarité et une plus grande stabilité, ce qui les rend idéales pour les applications où la précision est primordiale.
Intégrer les capteurs infrarouges pour les mesures sans contact
Les capteurs de température infrarouges, également appelés pyromètres, offrent une solution unique pour mesurer la température sans contact direct avec l'objet ou le matériau cible. Ces capteurs détectent le rayonnement thermique émis par les objets et le convertissent en une mesure de température.
Cette technologie est particulièrement utile dans des situations où :
- Le contact direct avec l'objet à mesurer est impossible ou indésirable
- La température de surfaces en mouvement doit être mesurée
- Une réponse rapide est nécessaire pour détecter des changements soudains de température
Les capteurs infrarouges trouvent des applications dans divers domaines, de la surveillance des processus industriels à la détection d'incendie, en passant par les diagnostics médicaux non invasifs. Leur capacité à fournir des mesures à distance les rend particulièrement précieux dans les environnements dangereux ou difficiles d'accès.
La technologie infrarouge a révolutionné la mesure de température dans de nombreux secteurs, permettant des contrôles de qualité et une surveillance des processus qui étaient auparavant impossibles ou extrêmement difficiles à réaliser.
Identifier les principales applications industrielles
Les capteurs de température jouent un rôle crucial dans de nombreux secteurs industriels, assurant la qualité, la sécurité et l'efficacité des processus. Leur utilisation s'étend bien au-delà de la simple mesure, influençant directement la productivité et la conformité réglementaire dans divers domaines.
Contrôler la température dans les lignes de production
Dans les environnements de production, le contrôle précis de la température est souvent synonyme de qualité du produit final. Que ce soit dans l'industrie automobile, électronique ou textile, les capteurs de température veillent à ce que chaque étape du processus de fabrication se déroule dans des conditions thermiques optimales.
Par exemple, dans l'industrie plastique, la température des extrudeuses et des moules d'injection est critique pour obtenir des pièces de qualité. Des capteurs de température stratégiquement placés permettent un contrôle en temps réel, assurant que le plastique fondu atteint et maintient la température idéale tout au long du processus de moulage.
De même, dans l'industrie métallurgique, les capteurs de température sont essentiels pour surveiller les processus de trempe et de recuit, garantissant que les propriétés mécaniques des métaux répondent aux spécifications requises.
Surveiller les systèmes de chauffage et de ventilation
Les systèmes de chauffage, ventilation et climatisation (CVC) dépendent fortement des capteurs de température pour maintenir un environnement confortable et sain dans les bâtiments. Ces capteurs sont les yeux et les oreilles des systèmes de gestion technique du bâtiment, permettant une régulation efficace de la température intérieure.
Dans les grands espaces commerciaux ou les complexes industriels, les capteurs de température sont répartis stratégiquement pour créer des zones de contrôle. Cette approche permet une gestion énergétique optimisée, adaptant le chauffage ou le refroidissement en fonction de l'occupation et des besoins spécifiques de chaque zone.
L'intégration de capteurs de température dans les systèmes CVC modernes permet également de mettre en œuvre des stratégies de contrôle prédictif . En analysant les tendances de température et en prenant en compte des facteurs externes comme la météo, ces systèmes peuvent anticiper les besoins en chauffage ou en refroidissement, optimisant ainsi la consommation énergétique.
Optimiser les processus dans l'agroalimentaire
Dans l'industrie agroalimentaire, la maîtrise de la température est cruciale à chaque étape, de la production à la distribution. Les capteurs de température jouent un rôle vital dans la sécurité alimentaire et la qualité des produits.
Lors de la transformation des aliments, les capteurs veillent à ce que les températures de cuisson, de refroidissement et de stockage soient maintenues dans les plages sécuritaires, prévenant ainsi la croissance de bactéries pathogènes. Par exemple, dans les processus de pasteurisation, des capteurs de haute précision assurent que le lait atteint la température requise pendant le temps nécessaire pour éliminer les micro-organismes nocifs.
Dans la chaîne du froid, les capteurs de température sont essentiels pour maintenir l'intégrité des produits périssables. Des systèmes de surveillance continue, souvent équipés de capteurs sans fil
, permettent de suivre la température des produits tout au long de leur transport et de leur stockage, garantissant leur qualité jusqu'au consommateur final.
Assurer la fiabilité et la performance des capteurs
La fiabilité des capteurs de température est primordiale pour garantir l'efficacité et la sécurité des processus industriels. Une mesure inexacte peut entraîner des défauts de production, des gaspillages énergétiques, voire des situations dangereuses. Pour maintenir des performances optimales, plusieurs aspects doivent être pris en compte, de l'étalonnage régulier à la protection contre les conditions environnementales hostiles.
Effectuer un étalonnage régulier pour garantir la justesse
L'étalonnage est un processus crucial pour maintenir la précision des capteurs de température au fil du temps. Il consiste à comparer les mesures du capteur à celles d'un étalon de référence et à ajuster le capteur si nécessaire. La fréquence d'étalonnage dépend de plusieurs facteurs, notamment le type de capteur, son environnement d'utilisation et les exigences de précision de l'application.
Pour effectuer un étalonnage efficace, suivez ces étapes :
- Déterminez la plage de température à étalonner en fonction de l'utilisation du capteur.
- Choisissez un étalon de référence certifié avec une précision supérieure à celle du capteur à étalonner.
- Effectuez des mesures à plusieurs points de température couvrant la plage d'utilisation du capteur.
- Comparez les lectures du capteur avec celles de l'étalon et notez les écarts.
- Ajustez le capteur ou sa courbe de calibration si les écarts dépassent les tolérances acceptables.
Il est important de noter que certains capteurs modernes, notamment les capteurs intelligents
, offrent des fonctionnalités d'auto-étalonnage ou d'étalonnage à distance, simplifiant considérablement ce processus.
Protéger les capteurs contre les conditions extrêmes
Les capteurs de température sont souvent exposés à des conditions environnementales difficiles qui peuvent affecter leur précision et leur durée de vie. La protection de ces dispositifs sensibles est donc essentielle pour maintenir leur fiabilité à long terme.
Plusieurs stratégies peuvent être mises en œuvre pour protéger les capteurs :
- Utilisation de boîtiers étanches pour protéger contre l'humidité et les projections
- Installation de filtres pour prévenir la contamination par des particules
- Mise en place de systèmes de refroidissement pour les environnements à haute température
- Application de revêtements spéciaux résistants à la corrosion
Dans les environnements chimiques agressifs, des matériaux résistants comme l'acier inoxydable ou le titane sont privilégiés pour la construction des capteurs. Pour les applications à haute température, des gaines de protection en céramique peuvent être utilisées pour isoler le capteur des chaleurs extrêmes.
La protection adéquate des capteurs n'est pas seulement une question de durabilité, mais aussi de sécurité et de conformité réglementaire dans de nombreux secteurs industriels.
Choisir des matériaux adaptés à l'environnement d'utilisation
Le choix des matériaux pour les capteurs de température est crucial pour assurer leur performance et leur longévité dans des environnements spécifiques. Chaque type d'application présente ses propres défis, qu'il s'agisse de résistance chimique, de conductivité thermique ou de stabilité à long terme.
Pour les applications en milieu corrosif, des alliages spéciaux comme l'Hastelloy ou l'Inconel sont souvent utilisés en raison de leur excellente résistance à la corrosion. Dans les environnements à haute température, des céramiques techniques comme l'alumine ou le carbure de silicium peuvent être préférées pour leur stabilité thermique.
La sélection des matériaux doit également prendre en compte les réglementations spécifiques à certains secteurs, comme l'industrie alimentaire ou pharmaceutique, où la biocompatibilité et la non-toxicité sont primordiales.