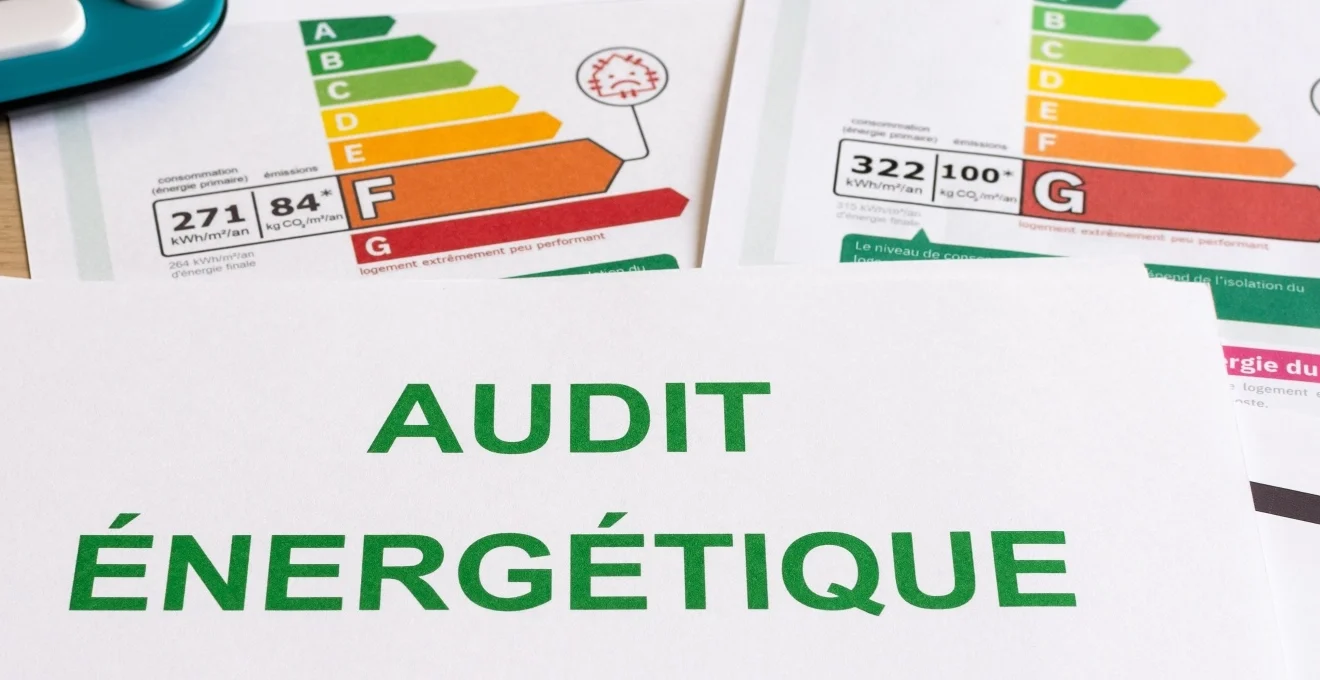
Dans un contexte de transition énergétique et de pression croissante sur les coûts, l'optimisation de la performance énergétique est devenue un enjeu majeur pour les industries. L'audit énergétique industriel s'impose comme un outil incontournable pour identifier les gisements d'économies d'énergie et améliorer l'efficacité des processus. Cette démarche structurée permet non seulement de réduire la facture énergétique, mais aussi de renforcer la compétitivité et de diminuer l'empreinte carbone des sites industriels.
Méthodologie de l'audit énergétique industriel selon la norme NF EN 16247
La réalisation d'un audit énergétique réglementaire en industrie suit une méthodologie rigoureuse définie par la norme NF EN 16247. Cette approche structurée garantit l'exhaustivité et la fiabilité des résultats obtenus. L'audit se déroule généralement en plusieurs phases clés :
- Collecte des données de consommation et analyse préliminaire
- Visite détaillée du site et des installations
- Mesures et relevés in situ
- Analyse approfondie des flux énergétiques
- Élaboration de recommandations chiffrées
La norme fixe également des exigences en termes de compétences des auditeurs et de qualité du rapport final. Elle impose notamment une revue critique des résultats par un expert indépendant pour les audits de grande envergure. Cette méthodologie éprouvée permet d'obtenir une vision globale et objective de la performance énergétique d'un site industriel.
L'audit énergétique ne doit pas être perçu comme une contrainte réglementaire, mais comme une véritable opportunité d'amélioration continue et de gains de compétitivité.
Analyse des flux énergétiques et bilan thermique des procédés industriels
L'analyse détaillée des flux énergétiques constitue le cœur de l'audit. Elle permet d'identifier précisément les postes les plus énergivores et de quantifier les pertes thermiques. Cette étape cruciale repose sur plusieurs outils et techniques complémentaires.
Cartographie des consommations par usage et par équipement
La première étape consiste à dresser une cartographie exhaustive des consommations énergétiques du site. Chaque équipement et chaque process sont passés au crible pour déterminer leur consommation spécifique. Cette analyse fine permet d'identifier les usages énergétiques significatifs qui concentrent la majorité des dépenses. La répartition entre les différentes formes d'énergie (électricité, gaz, vapeur, etc.) est également étudiée.
Mesures in situ et instrumentation temporaire
Pour affiner l'analyse, des campagnes de mesures sont réalisées directement sur le site. Des analyseurs de réseau électrique permettent de suivre en temps réel la consommation des équipements. Des caméras thermiques sont utilisées pour détecter les pertes de chaleur au niveau des fours, des canalisations ou des bâtiments. Cette instrumentation temporaire fournit des données précieuses sur le fonctionnement réel des installations.
Modélisation des pertes thermiques et calcul des rendements énergétiques
À partir des données collectées, les auditeurs modélisent les flux thermiques et calculent les rendements énergétiques des principaux équipements. Cette analyse permet d'identifier les sources de pertes et de quantifier les potentiels d'amélioration. Les outils de simulation numérique sont de plus en plus utilisés pour affiner ces calculs, notamment pour les process complexes.
Identification des gisements d'économies d'énergie prioritaires
L'analyse croisée de ces différents éléments permet d'identifier les gisements d'économies d'énergie les plus prometteurs. Les auditeurs hiérarchisent ces opportunités en fonction de leur potentiel d'économies, de leur faisabilité technique et de leur rentabilité économique. Cette priorisation est essentielle pour cibler les actions à fort impact.
Solutions techniques d'optimisation énergétique pour l'industrie
Une fois les gisements d'économies identifiés, l'audit énergétique propose des solutions techniques concrètes pour optimiser la performance énergétique du site. Ces préconisations s'appuient sur les meilleures technologies disponibles et sur le retour d'expérience des auditeurs.
Récupération de chaleur fatale sur les fumées et eaux usées
La récupération de chaleur fatale représente souvent un potentiel important d'économies. Les fumées des fours et chaudières, ainsi que les eaux usées des process, contiennent une énergie thermique qui peut être valorisée. Des échangeurs de chaleur permettent de récupérer cette énergie pour préchauffer l'air de combustion, l'eau sanitaire ou les fluides de process. Le taux de récupération
peut atteindre 60 à 80% selon les configurations.
Isolation thermique des réseaux de fluides et des équipements
L'amélioration de l'isolation thermique des équipements et des réseaux de distribution de fluides (vapeur, eau chaude, air comprimé) permet de réduire significativement les déperditions. Les nouvelles technologies d'isolants comme les aérogels offrent des performances remarquables. Une bonne isolation peut générer jusqu'à 20% d'économies sur la consommation de chaleur.
Régulation et pilotage intelligent des utilités (air comprimé, vapeur, froid)
L'optimisation de la régulation des utilités industrielles constitue un levier majeur d'économies. La mise en place de systèmes de gestion technique centralisée (GTC) permet d'ajuster finement la production aux besoins réels. Pour l'air comprimé par exemple, une régulation intelligente peut réduire la consommation de 15 à 30%. Le pilotage prédictif basé sur l'intelligence artificielle ouvre de nouvelles perspectives d'optimisation.
Remplacement des moteurs par des modèles à haut rendement IE3/IE4
Les moteurs électriques représentent souvent plus de 60% de la consommation électrique d'un site industriel. Le remplacement des anciens moteurs par des modèles à haut rendement de classe IE3 ou IE4 permet de réduire significativement cette consommation. Les économies peuvent atteindre 5 à 10% de la consommation électrique totale du site.
L'optimisation énergétique ne se limite pas aux équipements, elle passe aussi par l'amélioration des process et la sensibilisation des opérateurs.
Étude technico-économique et plan d'actions chiffré
L'audit énergétique ne se contente pas d'identifier des solutions techniques, il fournit également une analyse économique détaillée pour guider la prise de décision. Cette étude technico-économique est essentielle pour prioriser les investissements et construire un plan d'actions pertinent.
Calcul du temps de retour sur investissement des mesures préconisées
Pour chaque solution proposée, les auditeurs calculent le temps de retour sur investissement (TRI). Ce calcul prend en compte le coût des équipements, les frais d'installation, les économies générées et l'évolution prévisionnelle du prix de l'énergie. Le TRI permet de hiérarchiser les actions en fonction de leur rentabilité. Les mesures à TRI court (moins de 2 ans) sont généralement privilégiées dans un premier temps.
Estimation des économies d'énergie et réduction des émissions de CO2
L'audit quantifie précisément les économies d'énergie attendues pour chaque action, en kWh et en euros. La réduction des émissions de CO2 associée est également calculée. Ces données permettent d'évaluer l'impact global du plan d'actions sur la performance énergétique et environnementale du site. Elles sont essentielles pour le reporting RSE de l'entreprise.
Hiérarchisation des actions et phasage pluriannuel des travaux
Sur la base de l'analyse technico-économique, les auditeurs proposent un plan d'actions hiérarchisé et phasé dans le temps. Ce plan tient compte des contraintes budgétaires, techniques et organisationnelles de l'entreprise. Il permet d'échelonner les investissements sur plusieurs années tout en maximisant les gains. Un tableau de bord de suivi est généralement fourni pour piloter la mise en œuvre du plan.
Dispositifs de financement et aides mobilisables (CEE, ADEME, BPI france)
L'audit énergétique identifie également les dispositifs de financement et les aides mobilisables pour soutenir la mise en œuvre du plan d'actions. Les Certificats d'Économies d'Énergie
(CEE) constituent souvent une source de financement importante. Les aides de l'ADEME et les prêts verts de BPI France peuvent également être sollicités. Ces dispositifs permettent d'améliorer significativement la rentabilité des projets.
Mise en place d'un système de management de l'énergie ISO 50001
Au-delà des actions techniques, l'audit énergétique peut recommander la mise en place d'un système de management de l'énergie conforme à la norme ISO 50001. Cette démarche structurée permet d'inscrire l'amélioration de la performance énergétique dans une logique d'amélioration continue.
La norme ISO 50001 repose sur le principe du Plan-Do-Check-Act (PDCA) et impose la mise en place d'indicateurs de performance énergétique (IPÉ) suivis dans le temps. Elle implique également la formation et la sensibilisation du personnel à tous les niveaux de l'organisation.
La certification ISO 50001 apporte plusieurs avantages :
- Une réduction durable des consommations énergétiques
- Une meilleure maîtrise des risques liés à l'approvisionnement énergétique
- Une valorisation de l'image de l'entreprise auprès des parties prenantes
- Une exemption de l'obligation d'audit énergétique réglementaire
La mise en place d'un SMÉ ISO 50001 nécessite généralement l'accompagnement d'un expert pour structurer la démarche et former les équipes. L'audit énergétique constitue une excellente base de départ pour initier cette démarche.