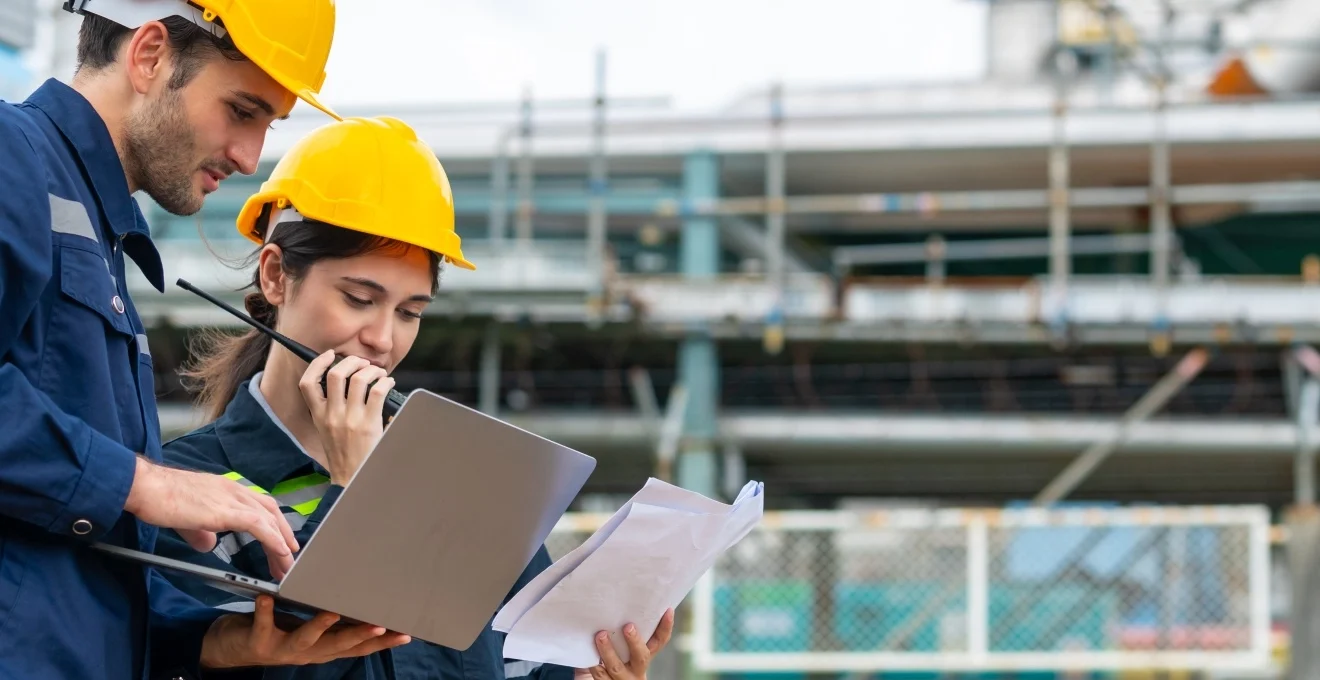
La maintenance industrielle joue un rôle crucial dans l'optimisation de la performance et de la longévité des équipements. En adoptant des stratégies avancées et des technologies innovantes, les entreprises peuvent significativement améliorer la rentabilité de leurs actifs industriels. Cette approche proactive permet non seulement de réduire les temps d'arrêt imprévus, mais aussi d'optimiser les coûts opérationnels à long terme. L'évolution vers une maintenance intelligente et prédictive transforme la manière dont les industries gèrent leurs équipements, ouvrant la voie à une efficacité accrue et à une compétitivité renforcée sur le marché mondial.
Stratégies de maintenance prédictive pour optimiser la durée de vie des équipements
La maintenance prédictive représente une avancée majeure dans la gestion des équipements industriels. Cette approche utilise des technologies de pointe pour anticiper les défaillances avant qu'elles ne se produisent, permettant ainsi d'intervenir de manière ciblée et efficace. En optimisant la durée de vie des équipements, les entreprises peuvent réaliser des économies substantielles tout en améliorant leur productivité globale.
Analyse vibratoire et détection précoce des défaillances mécaniques
L'analyse vibratoire est une technique puissante pour détecter les anomalies mécaniques à un stade précoce. En surveillant les vibrations des machines, il est possible d'identifier des problèmes tels que des désalignements, des déséquilibres ou des défauts de roulements bien avant qu'ils ne causent des dommages importants. Cette méthode permet d'intervenir de manière préventive, réduisant ainsi les coûts de réparation et les temps d'arrêt.
Thermographie infrarouge pour identifier les surchauffes anormales
La thermographie infrarouge est un outil précieux pour détecter les surchauffes anormales dans les équipements électriques et mécaniques. En visualisant les variations de température, les techniciens peuvent repérer des problèmes potentiels tels que des connexions électriques desserrées ou des composants surchargés. Cette technique non invasive permet d'effectuer des inspections sans interrompre le fonctionnement des équipements, contribuant ainsi à une maintenance plus efficace et moins perturbatrice.
Utilisation de l'intelligence artificielle dans la prédiction des pannes
L'intelligence artificielle (IA) révolutionne la maintenance prédictive en analysant de vastes quantités de données pour identifier des modèles et prédire les défaillances avec une précision remarquable. Les algorithmes d'apprentissage automatique peuvent traiter des informations provenant de multiples sources, telles que les capteurs, les historiques de maintenance et les données de production, pour générer des prévisions fiables sur l'état futur des équipements. Cette approche permet une planification plus intelligente des interventions de maintenance, optimisant ainsi l'utilisation des ressources.
Mise en place de capteurs IoT pour le suivi en temps réel
L'Internet des Objets (IoT) transforme la surveillance des équipements industriels en permettant un suivi en temps réel de leur état de fonctionnement. Des capteurs connectés collectent en permanence des données sur divers paramètres tels que la température, la pression, les vibrations et la consommation d'énergie. Ces informations sont transmises à des systèmes centralisés pour une analyse immédiate, permettant une réaction rapide en cas d'anomalie détectée. L'intégration de l'IoT dans la maintenance industrielle ouvre la voie à une gestion plus proactive et efficiente des équipements.
Planification et ordonnancement des interventions de maintenance
Une planification et un ordonnancement efficaces des interventions de maintenance sont essentiels pour maximiser la disponibilité des équipements tout en minimisant les perturbations opérationnelles. Cette approche stratégique permet d'optimiser l'utilisation des ressources humaines et matérielles, contribuant ainsi à réduire les coûts et à améliorer la productivité globale de l' entreprise de maintenance . La mise en place de systèmes de gestion avancés et la formation du personnel sont des éléments clés pour réussir dans ce domaine.
Méthodologie GMAO (gestion de maintenance assistée par ordinateur)
La GMAO est un outil fondamental pour la planification et le suivi des activités de maintenance. Ce système informatisé permet de centraliser toutes les informations relatives aux équipements, aux interventions planifiées et aux historiques de maintenance. Grâce à la GMAO, les gestionnaires peuvent optimiser les calendriers d'intervention, suivre les indicateurs de performance et générer des rapports détaillés. L'utilisation efficace de la GMAO contribue à une meilleure prise de décision et à une gestion plus proactive de la maintenance.
Optimisation des stocks de pièces détachées
Une gestion efficiente des stocks de pièces détachées est cruciale pour assurer la réactivité des interventions de maintenance. L'optimisation des inventaires permet de réduire les coûts de stockage tout en garantissant la disponibilité des pièces essentielles. Des techniques avancées d'analyse prédictive peuvent être utilisées pour anticiper les besoins en pièces détachées, évitant ainsi les ruptures de stock ou les excédents coûteux. Cette approche contribue à améliorer la performance globale de la maintenance industrielle.
Formation des équipes à la maintenance autonome
La maintenance autonome est un concept clé de la Total Productive Maintenance (TPM) qui vise à impliquer les opérateurs dans les tâches de maintenance de base. En formant les équipes de production à effectuer des inspections routinières, des nettoyages et des ajustements simples, les entreprises peuvent réduire la charge de travail des équipes de maintenance spécialisées. Cette approche favorise une détection plus rapide des anomalies et renforce la responsabilisation des opérateurs vis-à-vis de l'état des équipements qu'ils utilisent quotidiennement.
Analyse des coûts et ROI de la maintenance industrielle
L'évaluation précise des coûts et du retour sur investissement (ROI) de la maintenance industrielle est essentielle pour justifier les dépenses et optimiser les stratégies. Une analyse approfondie permet de quantifier les bénéfices tangibles et intangibles des initiatives de maintenance, facilitant ainsi la prise de décisions éclairées sur les investissements futurs. Cette démarche analytique contribue à aligner les objectifs de maintenance avec les objectifs stratégiques de l'entreprise.
Calcul du taux de rendement synthétique (TRS)
Le taux de rendement synthétique (TRS) est un indicateur clé de performance qui mesure l'efficacité globale des équipements. Il prend en compte trois facteurs principaux : la disponibilité, la performance et la qualité. Le calcul du TRS permet d'identifier les domaines d'amélioration potentiels et de quantifier l'impact des initiatives de maintenance sur la productivité. Un TRS élevé est généralement synonyme d'une maintenance efficace et d'une utilisation optimale des ressources.
Évaluation du coût total de possession (TCO) des équipements
Le coût total de possession (TCO) est un concept essentiel pour évaluer la rentabilité à long terme des équipements industriels. Il englobe non seulement le coût d'acquisition initial, mais aussi tous les coûts associés à l'exploitation, la maintenance et l'élimination de l'équipement sur l'ensemble de son cycle de vie. L'analyse du TCO permet de prendre des décisions plus éclairées sur les investissements en équipements et les stratégies de maintenance, en tenant compte de l'impact financier global sur le long terme.
Benchmarking des performances de maintenance par secteur industriel
Le benchmarking des performances de maintenance permet aux entreprises de comparer leurs pratiques et résultats avec ceux de leurs pairs dans le même secteur industriel. Cette analyse comparative fournit des insights précieux sur les meilleures pratiques du marché et aide à identifier les domaines d'amélioration potentiels. En se mesurant aux leaders de l'industrie, les entreprises peuvent fixer des objectifs ambitieux mais réalistes pour leurs programmes de maintenance.
Technologies émergentes pour la maintenance 4.0
La maintenance 4.0, alignée sur les principes de l'Industrie 4.0, exploite les technologies émergentes pour transformer radicalement les pratiques de maintenance industrielle. Ces innovations permettent une approche plus intelligente, connectée et prédictive de la gestion des équipements, ouvrant la voie à une efficacité opérationnelle sans précédent et à une réduction significative des temps d'arrêt imprévus.
Réalité augmentée pour l'assistance technique à distance
La réalité augmentée (RA) révolutionne l'assistance technique en maintenance industrielle. Cette technologie permet aux techniciens sur site de recevoir un support visuel en temps réel d'experts distants, superposant des instructions, des schémas ou des annotations directement sur leur champ de vision. La RA facilite la résolution rapide des problèmes complexes, réduit les erreurs et améliore l'efficacité des interventions, même pour les techniciens moins expérimentés.
Jumeaux numériques pour la simulation des interventions
Les jumeaux numériques sont des répliques virtuelles d'équipements physiques qui permettent de simuler et d'optimiser les interventions de maintenance avant leur exécution réelle. Cette technologie offre la possibilité de tester différents scénarios de maintenance, d'évaluer leur impact et de planifier les interventions de manière plus précise. Les jumeaux numériques contribuent à réduire les risques, à optimiser les ressources et à améliorer la qualité des interventions de maintenance.
Robotique collaborative pour les inspections en milieux dangereux
La robotique collaborative, ou cobotique, trouve des applications croissantes dans la maintenance industrielle, particulièrement pour les inspections en milieux dangereux ou difficiles d'accès. Ces robots peuvent travailler en harmonie avec les humains, effectuant des tâches d'inspection précises et répétitives tout en réduisant l'exposition des travailleurs aux risques. L'utilisation de robots collaboratifs permet d'améliorer la sécurité, la précision et l'efficacité des opérations de maintenance dans des environnements industriels complexes.
Normes et certifications en maintenance industrielle
L'adhésion aux normes et l'obtention de certifications en maintenance industrielle sont cruciales pour garantir l'excellence opérationnelle et la conformité réglementaire. Ces standards fournissent un cadre structuré pour l'amélioration continue des pratiques de maintenance, renforçant ainsi la fiabilité des équipements et la sécurité des opérations. Les entreprises qui investissent dans ces certifications démontrent leur engagement envers la qualité et l'efficacité de leurs processus de maintenance.
ISO 55000 pour la gestion des actifs industriels
La norme ISO 55000 établit un cadre international pour la gestion optimale des actifs physiques tout au long de leur cycle de vie. Elle fournit des lignes directrices pour développer une stratégie de gestion des actifs alignée sur les objectifs organisationnels. L'adoption de cette norme permet aux entreprises d'améliorer la performance de leurs actifs, de réduire les coûts opérationnels et de mieux gérer les risques associés à leur utilisation et leur maintenance.
Certification AFNOR en fiabilité des équipements
La certification AFNOR en fiabilité des équipements valide l'expertise des professionnels dans l'application des méthodes et outils d'amélioration de la fiabilité. Cette certification reconnaît la capacité à mettre en œuvre des stratégies efficaces pour optimiser la performance et la durée de vie des équipements industriels. Les entreprises employant des personnels certifiés AFNOR bénéficient d'une crédibilité accrue et d'une meilleure maîtrise de leurs processus de maintenance.
Méthode TPM (total productive maintenance) et ses piliers
La Total Productive Maintenance (TPM) est une approche globale visant à maximiser l'efficacité des équipements tout en impliquant l'ensemble du personnel. Cette méthode repose sur huit piliers fondamentaux : la maintenance autonome, la maintenance planifiée, l'amélioration ciblée, la formation et l'éducation, la gestion précoce des équipements, la qualité, la TPM dans les bureaux, et la sécurité, santé et environnement. L'application rigoureuse des principes TPM permet d'atteindre des niveaux élevés de productivité et de qualité tout en réduisant les coûts opérationnels.